Salient Features of Solid Propellant Rockets
Solid propellant rockets are the simplest of all rocket designs. They consist of a casing, usually, steel, filled with a mixture of solid compounds (fuel and oxidizer) that burn at a rapid rate, expelling hot gasses from a nozzle to produce thrust.
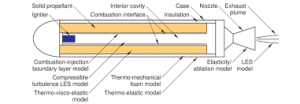
There are two families of solids propellants
- homogeneous
- composite.
Both types are dense, stable at ordinary temperatures, and easily storable.
Homogeneous propellants are either simple bases or double bases. A simple base propellant
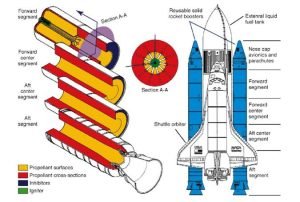
consists of a single compound, usually nitrocellulose, which has both an oxidation capacity and a reduced capacity. Double base propellants usually consist of nitrocellulose and nitroglycerine, to which a plasticizer is added. Homogeneous propellants do not usually have specific impulses greater than about 210 seconds under normal conditions. Their main asset is that they do not produce traceable fumes and are, therefore, commonly used in tactical weapons.
They are also often used to perform subsidiary functions such as jettisoning spent parts or separating one stage from another. Modern composite propellants are heterogeneous powders (mixtures) that use a crystallized or finely ground mineral salt as an oxidizer, often ammonium perchlorate, which constitutes between 60% and 90% of the mass of the propellant. The fuel itself is generally aluminum. The propellant is held together by a polymeric binder, usually polyurethane or polybutadienes, which is also consumed as fuel. Additional compounds are sometimes included, such as a catalyst to help increase the burning rate or other agents to make the powder easier to manufacture. The final product is a rubber-like substance with the consistency of a hard rubber eraser.
Composite propellants are often identified by the type of polymeric binder used. The two most common binders are polybutadiene acrylic acid acrylonitrile (PBAN) and hydroxy-terminator polybutadiene (HTPB). PBAN formulations give a slightly higher specific impulse, density, and burn rate than equivalent formulations using HTPB. However, PBAN propellant is more difficult to mix and process and requires an elevated curing temperature. HTPB binder is stronger and more flexible than the PBAN binder.
Both PBAN and HTPB formulations result in propellants that deliver excellent performance, have good mechanical properties, and offer potentially long burn times. Solid propellant motors have a variety of uses. Small solids often power the final stage of a launch vehicle or attach to payloads to boost them to higher orbits. Medium solids such as the Payload Assist Module (PAM) and the Inertial Upper Stage (IUS) provide the added boost to place satellites into geosynchronous orbit or on planetary trajectories.
Read More :
- what is a monoplane
- Airports Authority of India has released 400+ Air Traffic Control (ATC) Junior Executive posts
- Free Udemy Courses
If you liked this article about Solid Propellant Rockets, then please subscribe to our Newsletter for More Articles about aeronautical engineering. You can also find us on Instagram, , and Telegram.
7 Comments
Excellent
Pingback: How to Install Python on a Mac & Windows : A Step-by-Step Guide » The Skypedia
Pingback: The Top 6 Best Python IDEs for Enhanced Productivity in 2023 » The Skypedia
Pingback: Best Visual Studio Code Extensions for Web Developers » The Skypedia
Pingback: For web development, here's how to install VS CODE » The Skypedia
Pingback: Top 10 Aerospace Companies of the World » The Skypedia
Pingback: "The Engineering Handbook: The Essential Guide for Every Engineer" » The Skypedia